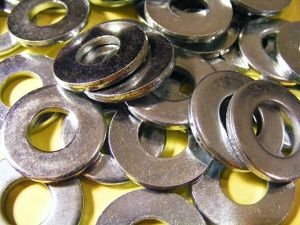
Many items need require a coating of metal. Such can be applied in a couple of ways. One way is electroless plating. Another way is electroplating.
Chrome handles on car doors are plastic with a veneer of metal. When you look in a mirror, you see your reflection in a sheet of glass with a metal film on the back. If you wear gold eyeglasses, there is a super thin coat of gold over base metal.
Most plating uses a water solution containing metal salts. If an electric source is used to deposit the plate, the process is electroplating. If no electric source is used, it is auto-catalytic or electroless plating.
How do these work? We will discuss the basics, beginning with electroplating.
Electroplating
Most often, a metal object is attached to a DC power supply. This object is carefully cleaned. It is then ready to be plated. It is immersed in the plating solution. A calculated current is applied. The correct current is related to the surface area of the piece.
Electrons flow into the piece. This draws metallic ions. These attach to the part as neutral atoms. The positive wire of the power supply is attached to the anode. It is usually a metal that does not dissolve such as titanium, or it is the same metal as that being plated. This replenishes the ions used up.
For copper plating, a copper salt and other chemicals are dissolved in water. The piece to be plated is connected to the negative wire. It is immersed in the bath. A bagged copper bar is attached to the positive wire and is also immersed. The bag prevents oxidized particles from contaminating the bath. The desired copper ions can and do escape through the fabric of the bag.
Stirring helps assure sufficient metal ions at the surface of the part. This is because metal ions are depleted in a very thin layer right at the surface of the part. Stirring replenishes them. Also, use of a brightener smooths the copper deposited. If needed, immersion heaters keep operation within an acceptable temperature range. For copper, this is pretty close to room temperature.
Electrical plating is quick. The bath tends to be stable. It is usually inexpensive. So why use electroless plating? There can be real advantages!
Electroless Plating
Electroless copper spreads plating uniformly. In electroplating, coating thickness varies from point-to-point.
Electroless plating requires no conductivity. Remember the mirror? One cannot hook wires to glass and expect metal to grow by electroplating. Glass is non-conductive! Recall the plastic automobile handles? Plastic does not conduct electricity.
How does one electrolessly plate parts? The key lies in the chemistry of the bath. The bath is unstable under certain conditions. One or more molecules within the bath attack other molecules. Often the reaction is an oxidation-reduction reaction. Bath instability is good in this case, but only under the proper conditions.
The part must first be cleaned. It is then immersed in a catalytic liquid. This adheres to the surface of the part. Excess is gently rinsed off. The part is immersed in the plating solution. The coating initiates an oxidation-reduction reaction. Metal deposits at the surface of the part. It adheres. It forms a coat.
The following video is guaranteed to absorb your attention. It demonstrates, without words, the process of electroless plate.
If this form of plating is so useful, why is electroplating preferred for many applications? Electroless plating has drawbacks. Generally, the bath must be heated. This causes evaporation. It adds a cost for energy.
The bath has a limited life time. The plated part may lose a little coating. Traces of material due to imperfect rinsing may cause metal particles to form in the bath. The bath plates these particles. This eventually destroy the bath. Very thorough filtration must be used.
Another fault is most electroless baths are useful only for very thin coats of metal. Electrical plating may need to be added to thicken the metal film. Also some metals do not readily lend themselves to electroless formulation.
Note: You might also enjoy Use of the Hull Cell in Maintaining Electroplating and Electroforming Baths
Researches:
I thought it was informative when you explained that metal objects are attached to a DC power supply when they are going through the process of electroplating. As far as I know, anytime an extra coat of material is added to metal, this is done so that it can be protected against corrosion and wear and tear. I would imagine that electroplating can make a metal more efficient for electrical purposes in things like vehicles and solar panels.
I found it interesting when you talked about electroplating and how it’s a fast and cost-effective option. In my opinion, business owners should explore their coating options before choosing one. If I were to run an automotive plant, I’d evaluate my needs and choose the right metal coating technique. Thanks for the information on how electroplating works.
Ah, but you do, right? Thanks for visiting.